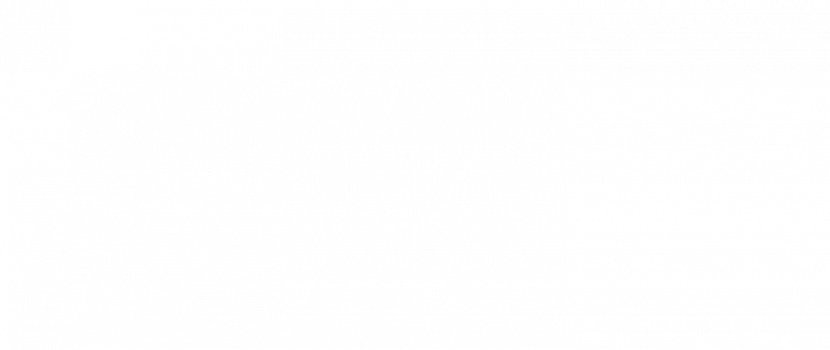
The Benefits of Copper for Plating PEEK and Ultem
When plating engineered polymers and resins like PEEK and Ultem, the benefits of copper include excellent electrical and thermal conductivity. What are the pros and cons of copper plating engineered plastics like the innovative polymers PEEK and Ultem?
In aerospace, medical, and industrial applications, copper can be used to add beneficial qualities like electrical conductivity, corrosion protection, and radiation reflection, to list a few.
Polyether Ether Ketone (PEEK) is an organic thermoplastic polymer in the PAEK—Polyaryletherketone—family. It offers high mechanical and chemical resistance, both of which can be sustained during high temperatures. With a melting point of 662 °F (343 °C) for certain PEEK variations, it is used in applications from aerospace technology to the medical field, including surgical implants. PEEK has a very high stress tolerance with a great degree of longevity.
The Benefits of Copper Plating
There are several “pros” that demonstrate the benefits of electroless copper plating on engineered plastics.
- Cost-efficiency: One of the benefits of copper plating is its low cost, compared to gold, silver, and palladium.
- Metallic qualities: With high plating efficiency and exceptional surface coverage, copper can be used to metalize any engineered plastics, adding electrical conductivity, as well as strengthening and protecting the substrate.
- Reflection of light and UV and infrared radiation: Copper can be used to reflect light and radiation away, protecting electronics and other sensitive materials.
- Facilitate the flow of electricity: Plating copper onto engineered plastics like PEEK and Ultem can also give a non-conductive plastic surface the ability to conduct electricity, a property that is invaluable to the manufacturers of electronic parts and components used in automobiles, aircraft, spacecraft, and a multitude of other products.
- Malleability: Copper plating is inherently flexible, allowing it to bend and maintain adhesion.
- Protective barrier: Copper is exceptionally resistant to corrosion and can be used to protect a substrate. To preserve the appearance, a clear coating can often be utilized.
- Polyetherimide (PEI)—referred to as Ultem—is a thermoplastic that can withstand high temperatures while functioning as an electrical conductor. It has the advantage of dynamic stability of its electrical properties, spanning over frequencies and temperatures. Ultem is commonly used in medical and chemical instruments and can be sterilized with gamma rays. Additional uses include components for engines in the automotive and aerospace industries.
Challenges of Copper Plating
While copper plating benefits are plentiful, as listed above, plating with copper or any metal can present its own set of “cons” or challenges. A few of the most common are listed here.
- Must follow precise criteria. When determining engineering specifications, the plating material must be considered. Detailed standards must be followed, or plating will fail. In just one example, a substrate design that doesn’t allow the liquid to flow freely through the part could cause the plating liquid to pool there.
- Complex surfaces can be challenging to plate evenly. Electroless copper plating is the process of choice when a component has demanding geometries. However, a substrate that requires sharp grooves, cavities, ribs, or closed rings may need to be redesigned to accommodate certain plating requirements.
- Avoiding contamination is critical. Any contamination on a substrate can lead to adhesion and surface defect issues with copper or any metal plating. While plating preparation includes specific chemical solution baths, any missteps on behalf of the plating operation can cause the plating to fail.
Copper Plating for PEEK and Ultem
At SAT Plating, our Surface Activation® technology was designed for plastics that had previously been considered “unplatable.” It allows us to achieve the industry’s most robust adhesion and process scalability. The finish and dimensions of the component are unchanged, unlike acid etching, media blasting, and plasma treating processes.
Learn more about it here: Surface Activation® technology at SAT Plating