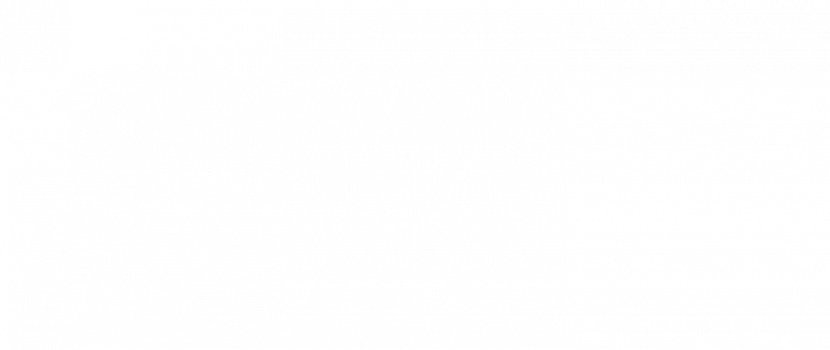
Plating Engineered Plastics – Avoid All The Headaches
Plating high-performance plastics presents challenges for which many engineers and product development teams are not prepared. High scrap rates and costly reworking of parts is a common story from those who have ventured down the plating path. Let’s explain the basics and keep your next project on track from day one.
Metals are better conductors
Unlike plastics, metals electroplate easily because they have natural conductivity. As plastics are not generally conductive, a plater must first form an initial thin layer of conductive metal on the polymer surface – usually @ 25,000 micro inches (.635 micron) thick.
This foundational layer is what plastic platers refer to as the “pre-plate” or “strike” layer. This is formed using electroless plating chemistry which affects metal formation through a catalytic reaction, typically triggered by palladium. Once this conductive metal layer is established thicker subsequent layers of other metals can be deposited on top using higher speed electrolytic methods.
Achieving high adhesion of the strike layer is critical. Any weakness in this foundation layer makes subsequent additions susceptible to failure. In fact, most plating defects start with a loss of adhesion at the interface of this first metal layer to the polymer.
Plating polymers is art and science
Today, there are tens of thousands of polymer blends and each one requires its own unique plating “recipe”. Some are extremely chemically resistant and require elaborate activation cycles. Some have modifying additives and fillers*, which can adversely impact metal adhesion. Others still are chemical resistant and have fillers, requiring even more elaborate processing.
Most platers of engineered plastics employ extraordinary surface preparation measures, such as media blasting, or chemical erosion, sometimes both, which adversely affects part dimensions and other characteristics. Even with these measures, the first-run plating fall-out can be astronomically high — upwards of 40%. The rejected parts are then reworked by repeating the same surface preparation. The results are even rougher, more eroded surfaces with rounded edges and distorted threads.
Surface Activation® gas technology
SAT Plating has proprietary Surface Activation® gas technology which delivers high adhesion at the atomic level atomic adhesion without aggressive chemical or mechanical etching of the substrate surface. Our proprietary capabilities allow us to plate the most advanced composite and high performance materials in the world. This is important when processing injection molded and rapid manufactured parts with fine features and dimensions, or films and fibers.
SUGGESTED READ: SAT Plating’s Proprietary Plating Technologies
Surface Activation®, along with our suite of Adaptive Plating Technologies®, allows us to achieve superior metal adhesion and bonding properties that meet the requirements for aerospace defense, medical, and industrial applications.