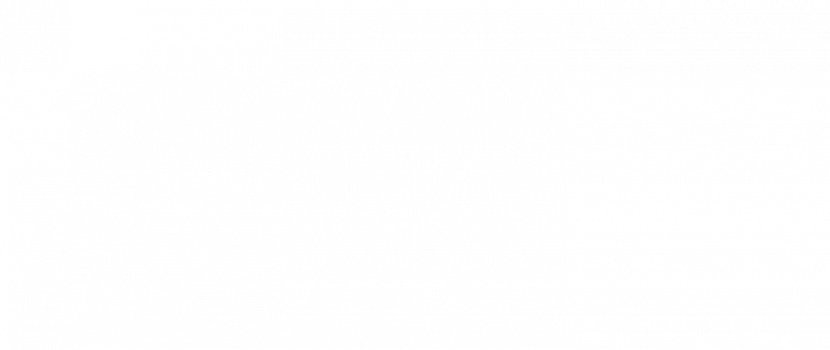
A Closer Look at Corrosion Resistance and Electroplating: Their Broad Spectrum of Applications
Corrosion resistance has always been a crucial part of Aerospace & Defense (A&D) development because of the extreme conditions that aircraft and military products are subject to. This property is essential as corrosion, a naturally occurring process, can lead to the degradation of critical materials over time, compromising their structural integrity and function. Especially aboard aircraft, components are frequently exposed to extreme conditions—varying temperatures, high pressures, and often saline or otherwise chemically aggressive environments. Such conditions can accelerate the rate of corrosion, which can be damaging to electronic components. As a result, developing materials with high corrosion resistance or implementing protective measures, such as coatings and treatments, is pivotal in mitigating these risks and ensuring the longevity and reliability of components and systems.
What is Corrosion Resistance?
Corrosion resistance is the capacity of a material to resist degradation due to its reaction with its surrounding environment. This ability is especially important in materials that are susceptible to rust, oxidation, or other forms of corrosive wear such as onboard electronics. In these cases where electronics are at risk, corrosion can have particularly devastating consequences. It can lead to electrical shorts, decreased conductivity, and eventual component or system failure. Such failures can be costly in terms of repairs and replacements, but they also pose serious safety risks, especially in mission-critical applications found in the A&D sector. To combat these threats, A&D manufacturers invest in corrosion-resistant housings to protect the components. These housings have protective features like coatings, treatments, and controlled environments, all aimed at extending component lifespan, preserving functionality, and ensuring safety.
The Science Behind Electroplating High-Performance Polymers
Electroplating polymers is a fascinating process where high-performance plastics are given a metallic coating using different electrical charges and plating science. In a typical setup at SAT, the plastic housings are submerged in a solution known as an electrolyte. When an electric current is introduced, metal ions from the source plating material, or the anode, are attracted and bonded to the surface of the housing we want to plate, known as the cathode. Delving deeper at the molecular level, the anode’s metal atoms dissolve into the solution as positively charged ions. These ions then travel toward the negatively charged cathode and gradually bond to its surface, forming a new metallic layer. When applied to performance plastics, the metallic layer can make them conductive or shield them from electromagnetic interference all while maintaining the inherent advantages of the plastic such as reduced weight and durability.
Key Benefits of Electroplating in the A&D Sector
Electroplating has become invaluable in the Aerospace and Defense sector, particularly when applied to performance plastics. First and foremost, it offers increased durability. Components in the A&D industry face extreme conditions, from high altitudes to engine heat. An electroplated metallic layer on plastics ensures these components can withstand such rigors, prolonging their lifespan. This becomes especially important when plastic housings are used to protect more delicate components from corrosion or EMI. The metallic coating applied to an engineered polymer such as PEEK, can eliminate corrosion or take the brunt of the impact. The enhanced conductivity of an electroplated plastic componentalso aids in integrating them into electronic systems without adding substantial weight, a process known as “lightweighting.”
Applications in Electronics Housing
In the Aerospace and Defense industry, electronics housings are crucial for safeguarding sensitive components against extreme operational conditions. Corrosion, induced by factors such as moisture, salinity, and chemicals, poses a significant threat to these housings and the electronics they protect. Electroplating enhances corrosion resistance by adding a protective metallic layer to the housing, simultaneously offering added benefits like thermal conductivity and electromagnetic interference shielding. This protective layer acts as a barrier, shielding both the housing material and the internal electronics from environmental damage, thereby ensuring the longevity and optimal functionality of electronic systems in aircraft.
The Future of Electroplating and Corrosion Resistance
The future of electroplating and corrosion resistance is marked by continuous innovation, driven by emerging trends and research. As the A&D sector pushes the boundaries of performance and durability, novel techniques and materials are being explored to amplify the benefits of electroplating. Advanced polymers combined with adaptive electroplating methods offer hydrophobic surfaces, minimizing wear and moisture-related issues. Additionally, research into more environmentally-friendly and efficient electroplating processes aligns with the global shift towards sustainability. As performance plastics play an increasingly pivotal role in A&D, these advancements will ensure they not only meet but anticipate and exceed industry demands, optimizing their utility in ever-evolving operational landscapes.
Conclusion
The potential risks posed by corrosion, especially in the demanding A&D environment, underscore the need for advanced protection mechanisms. Electroplating, with its ability to combine the strengths of metals and efficiencies of plastics, emerges as a potent solution. Ensuring that the A&D sector remains equipped with materials that are not just reactive but proactive in their defenses will be paramount in navigating the challenges and opportunities of tomorrow’s technological landscape. Selecting the right plating material for your electronic housing must be done with the help of experienced professionals like SAT Plating. SAT Plating can help companies with everything from R&D to high-volume manufacturing and shipping the finished product. Get in touch with our experts today to discuss your project’s requirements and how SAT can help meet specifications. We support programs with volumes as low as 1,000 parts to well over 1 million parts per year.