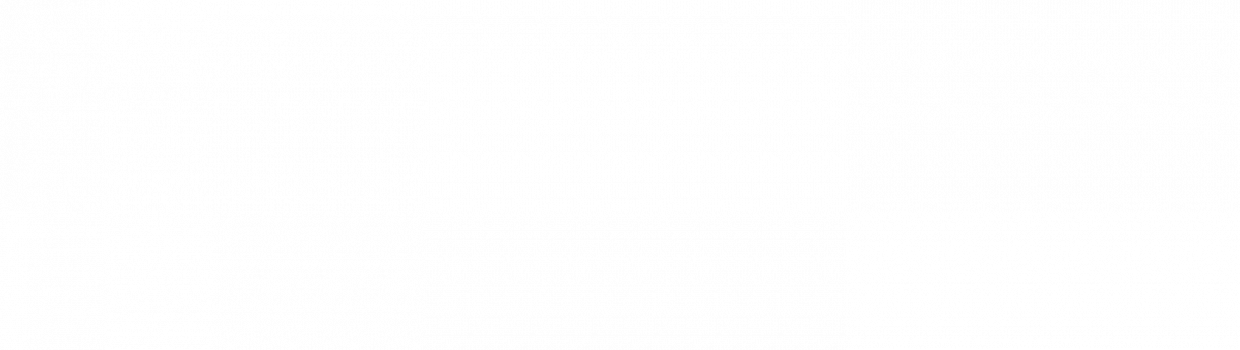
Welch Allyn Pro 6000 Ear Speculum Case Study
Welch Allyn was looking for a company capable of creating a long-lasting probe tip for their Pro 6000 Ear Speculum. They needed a company capable of plating the probe tip without compromising its already tight and sleek design, while also ensuring that the tip was durable. They needed a company that could plate the PC/ABS portion of the tip with a reliable and resilient adhesion. That’s where we stepped in to help.
The area we plated had a specific design that had to be adhered to. The tip would be inserted into a patient’s ear to gauge their temperature. The tip was required to be plated with three strips of different metal bands to accurately gauge the temperature of the patient at various locations within the patient’s ear. The tip would be molded from a multi-shot plastic component.
In order to accomplish our goal for Welch Allyn, we used a solution in which we pre-treated the plastics with our trademarked Surface Activation® Process. This process alters the surface of polymer without damaging it with abrasive blasts or hazardous chemicals. Due to this process, the PC/ABS can be plated without compromising the dimensions of the initial plastic component of the tip. With this, we helped usher in an advancement for speculum technology.
These advancements came from Welch Allyn’s desire to build a better speculum to help aid in the temperature taking process for the medical field.
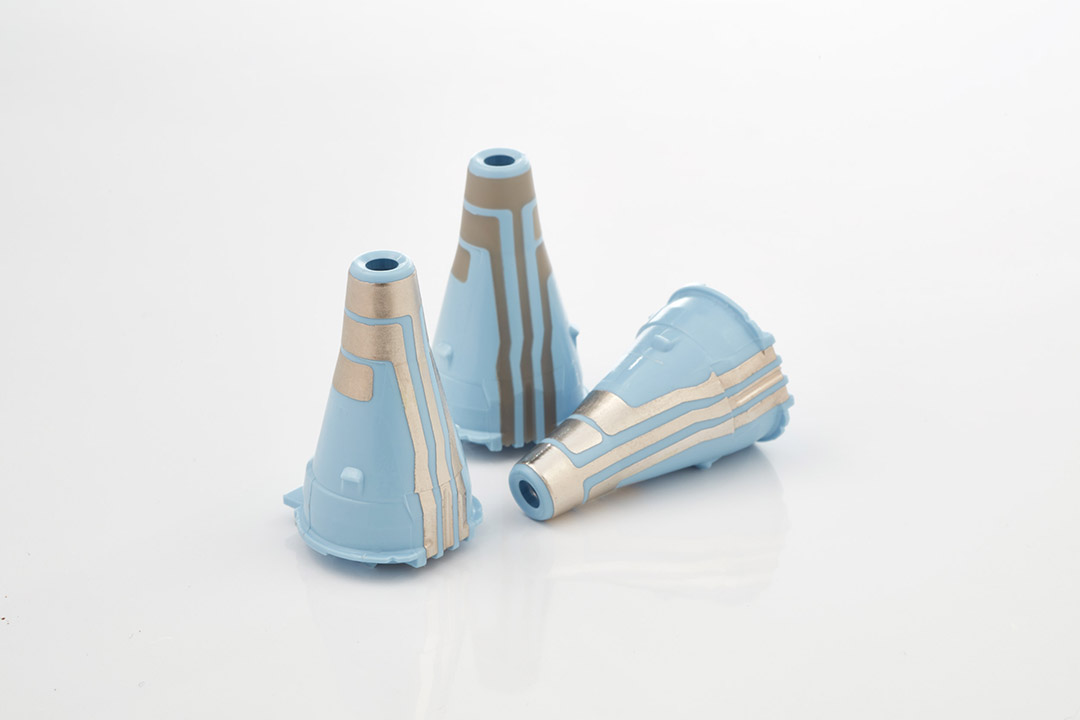
This medical advancement in plating, and other advancements like it, is all possible due to our SelectPlate™ process. This process affords us the ability to electroplate biocompatible polymers, which helps boast a base polymers already stellar set of characteristics. This process was driven by the constantly shifting landscape of the medical industry, which is always looking for more compact and efficient components for their devices. The performance limitations previously seen when attempting to plate biocompatible polymers is what peeked our desire to further the field, which helped us develop our SelectPlate™ process, ultimately removing the roadblocks that kept biocompatible polymer plating from reaching all new heights in potential.